Sodecia
anti-corrosion surface treatment
years of cooperation
realized projects
coated parts
About customer:
Sodecia Group is a global supplier of services in the field of production of chassis, fuel and bodywork for the automotive industry. Sodecia currently has 47 locations in 5 regions: in Europe, South America, North America, Africa and Asia-Pacific. In 2018 it employed more than 7300 employees throughout the world. Its total sales amounted to €831 million.
Sodecia – Lakum-KTL:
Lakum-KTL has been a supplier of surface finishes for Sodecia since it entered the Czech market in 2017. But the mutual cooperation of our firms dates back to 2006, when we established business relations with the “preacquisition” firm Kemmerich Czech. After the acquisition of the firm Kemmerich Czech by the multinational company Sodecia, the company Sodecia Safety & Interiors Leskovec, s.r.o. was established.
Aims and cooperation
In our business relationship Sodecia places long-term emphasis on the key points of cooperation:
● Reliability in adherence to delivery deadlines
● Price stability and attractive level of prices compared to the competition
● Operative approach to dealing with random events during production
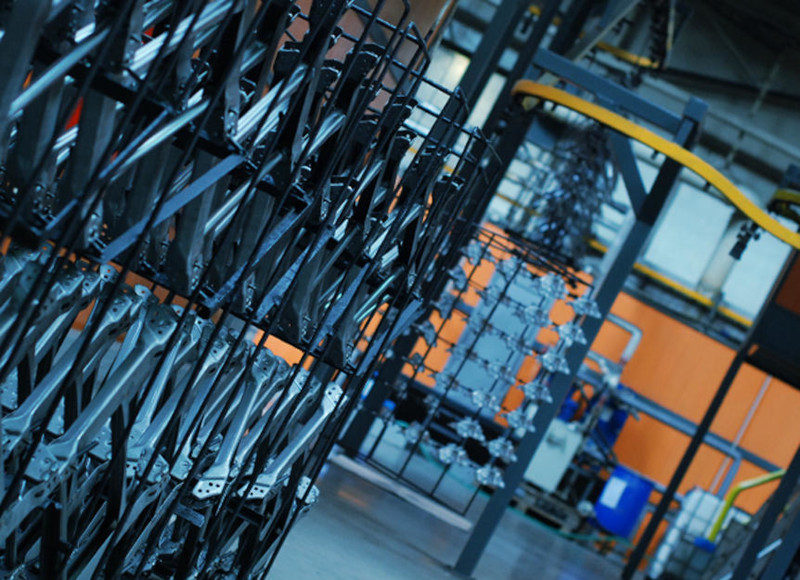
Since the start of our business relationship with the company Sodecia we have implemented 43 projects for leading automobile manufacturers. In practice, this means more than 25,963,583 surface finished parts.
Project of surface finish for mass produced parts:
End customer automobile producer FORD requires surface finish complying with high standards and norms. It involves a combination of two technological procedures:
● zinc electroplating according to standard FORD WSS-M1P85-B3
● cataphoretic painting according to standard FORD WSS-M2P177-C3
Project of surface finish of special material:
The requirement for coating of product Sodecia for AUDI was demanding in many respects. The product requires coating according to standard VW13750 Ofl x634 with minimum coating thickness of 35 microns. As this is a relatively large flat part, moreover made of the special material CR3-EG47/47-E-PO, coating in the required scope is technologically demanding. The preparation of the entire process required a large volume of sampling.
Thanks to the experience of our experts, we discovered during the sampling that the product is susceptible to scratching. We fine-tuned the parameters and details of the entire process. We included a completely new product packaging approach in the process, and damage has no longer occurred. Completed, coated components reach the end customer at the assembly site in good order and with no faults caused during transport.